Forest-based bioeconomy – Products and technologies
The main focus of ForestBioFacts is in providing the reader with an in-depth understanding of the technologies and processes used for the conversion of wood into a variety of industrial biomaterials and chemicals. Some biomaterials manufactured by the forest industry are consumer products like hygiene papers, while others are to be converted further by yet another industrial sector, e.g., contstruction sector, packaging and logistics, media and communications, the chemical industry, the food and beverages industry, pharmaceutical and cosmetics industries. In this brief article, only the basic ideas of some process concepts are introduced. Nevertheless, in-depth understanding of biomass conversion technologies comes in several layers of knowledge, as described in Figure 1.
By definition, technology means the application of scientific knowledge in practice, especially for industrial purposes1. In the case of thermochemical conversion of wood or other lignocellulosic biomass, the limiting factors in the process dynamics are usually related to the micro-scale structure of plant biomass, rather than to reaction kinetics as such. This is due to the composite polymeric structure of the cell wall, which is resistant to the penetration of cooking chemicals and also slows down the extraction of reaction products.
Hence, understanding the complex structure of biomass and its behaviour in process conditions is the basis of mastering biomass conversion processes like the manufacture of wood pulp or the extraction of valuable chemicals from wood. For the same reason, when developing new industrial biomass conversion processes or when introducing changes to existing ones, experimental R&D work and conceptual engineering are of great importance.
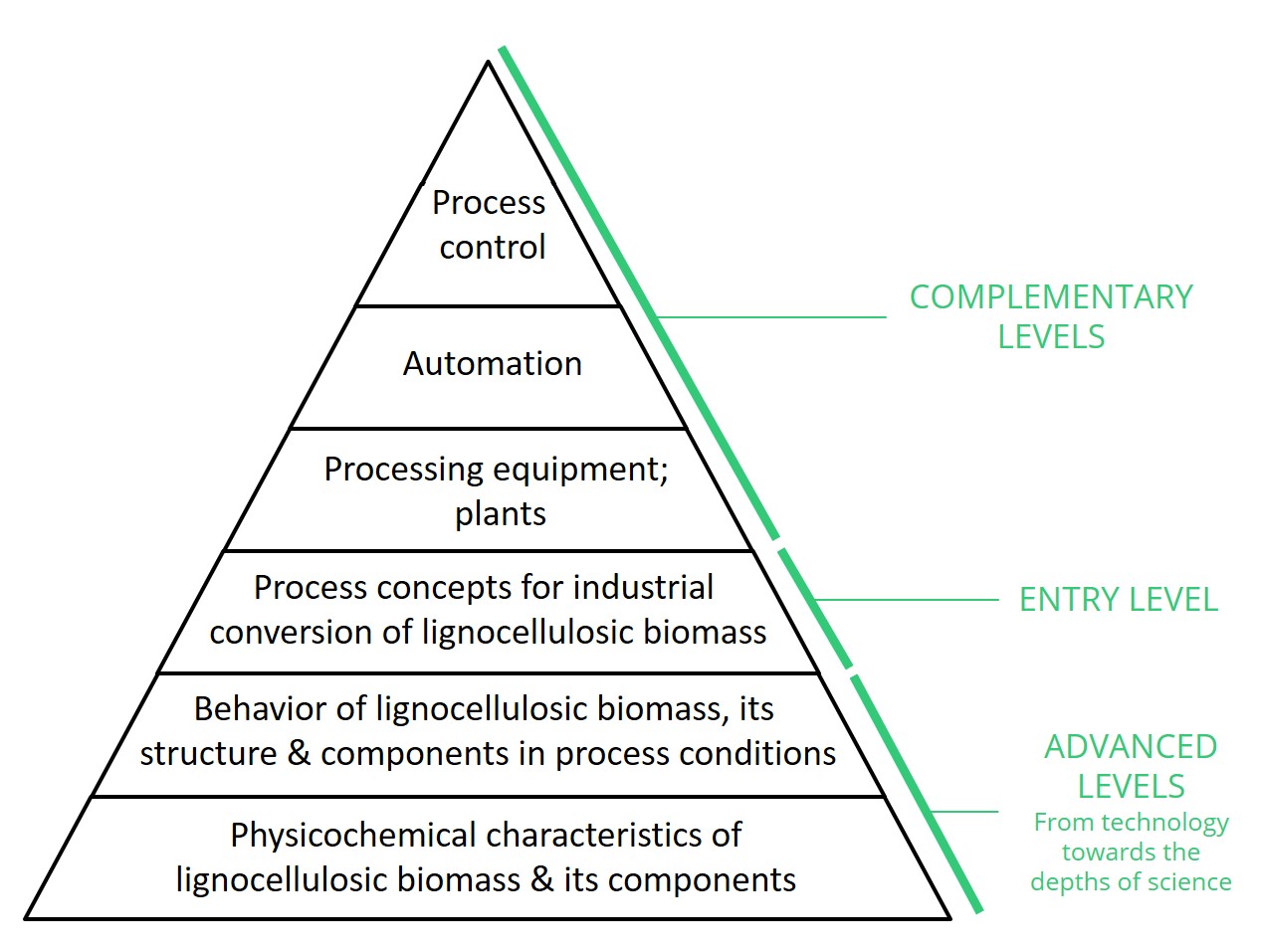
The conversion of wood into products like paper, packaging boxes or garments begins with the manufacture of fibre pulp. Targeted pulp properties depend strongly on the desired behaviour of pulp in the down-stream conversion process, or the pulp’s processability, and on its expected performance in the final product and end-use. Tissue paper makers and the end-user expect different performance of pulp fibre than the producer and the end-user of a cardboard box or a shiny magazine.
For pulp, which is converted into textile fibre for garment manufacture, good processability is everything, as no structural feature of pulp fibre can be recognised in the final product.
Pulping and biorefining processes
The three main constituents of wood are cellulose, lignin and hemicelluloses. Each of them has a different polymeric chemical structure and structural function in wood cells. Jointly they also form the sturdy composite macrostructure, which serves the tree in its stem, branches and roots. Pulp wood is usually so-called thinning wood or top parts of harvested logs, or it comes from plantations dedicated to pulpwood production. Also the left-over of sawn timber manufacture, or saw mill chips form an important source of pulp wood.
Prior to feeding wood into the actual pulping process, it is debarked and, with the exception of ground-wood pulp, cut into chips of controlled dimensions.
In order to utilise the fibrous micro-scale structures of wood, individual wood cells need to be detached from the macro-scale structure of the chips, and from each other, to make fibre pulp. This is done by suitable combinations of mechanical, thermal and chemical means, depending on the desired physical and chemical properties of the final fibre pulp. Enzyme treatment can also be used. In mechanical or thermomechanical pulping processes, the idea is to retain all three main constituents of wood in the final pulp, hence known as high-yield pulp.
The common target of chemical pulping processes is to retain the cellulosic part of wood cells intact while extracting lignin and, in some cases, also hemicelluloses out of the structure. To do this, different combinations of pre-hydrolysis, delignification (or cooking) and bleaching stages are needed depending on the targeted end-use application of the produced pulp.
A chemical pulp mill using the kraft process is a closely integrated combination of three parts. The first is the fibre line, the idea of which was outlined above. The second is the recovery boiler, where cooking chemicals are recovered and the dissolved lignin is utilised as a fuel to generate steam and electricity for all three parts of the mill, and the third is chemical regeneration, where used cooking chemicals are reactivated. In addition, some lignin may be isolated as a separate bio-product or used to generate carbon-neutral electricity for external customers. Also wood extractives, or pitch, is recovered as by-products. In addition to the kraft process, also different sulphite pulping processes are quite common, especially when textile grade pulp is produced.
For a good reason, pulp mills are also called wood-based biorefineries or bio-product mills. Also bleaching chemicals are often manufactured at the same mill site.
Different biomass fractionation processes are also developed, where alcohol or other solvents are used in the cooking liquor. The targeted benefits include, e.g., recovering lignin as a more reactive polymer, more simple chemical recovery and obtaining valuable hemicellulosic sugars in pure form at high yield. In such cases, fibre pulp with good paper-making properties is not the prime target, and also agricultural residues like various cereal straws can be used as the raw material.
Paper and board making
The basic concept of making paper or paper board is very simple: Fibre pulp is dispersed in water, spread evenly over a wire screen to drain the water, and the remaining water is removed by pressing and heating.
However, the modern paper machine is highly sophisticated set-up of process equipment to carry out those tasks efficiently at large scale. For instance, world’s fastest printing paper machines produce paper at the rate of 300 m2 per second, at high time and material efficiency, around-the-clock, around-the-year. The thickness of the product is c. 0.1 mm and the quality tolerances are tight, because the customer’s printing machine is also fast, and the printer is demanding on print quality. Indeed, large and fast paper and board machines demonstrate the highest level of the process control and automation employed in modern forest-based industries.
Listen to why Production Manager Jari Nikkinen from Sappi Europe considers that we still need paper.
From research to innovation
Driven by the advance of circular bioeconomy, new opportunities for growth and diversification are opening to forest-based industries. As a consequence, the demand for innovative technologies, processes, product and end-use application is high. Also new raw-materials, like agricultural residues, used cotton garments or bacterial cellulose are gaining growing interest.
R&D activities within the biomaterials industry are now more diversified than during the extended period of steady strong growth of printed media, which peaked at beginning of this new millennium. Large industrial companies and SMEs in this field, as well as at research institutes and universities, are all increasingly involved also in joint projects.
From research to industrial innovation
Industrial innovation is a commercialised novel idea. It may be a novel process concept or a new product, but more often it is an improvement to an existing industrial process, product or end-use application. In the context of industrial scale mill operations, especially in the case of new investments, managing the related risk is a key success factor for R&D and innovation projects. Failing to assess the risk in advance and preparing to manage it during the project may have costly consequences – or even prevent the entire project from being launched. Industrial innovations don’t happen without investments.
As explained in Figure 2., the key idea of managing the risk involved in industrial innovation and investment project is to bring down uncertainty before the financial exposure grows large. This is done by stepwise progress and involves technology transfer from the R&D team to the investment project team, and again to production and sales teams. Hence, good communication within and between teams is essential.
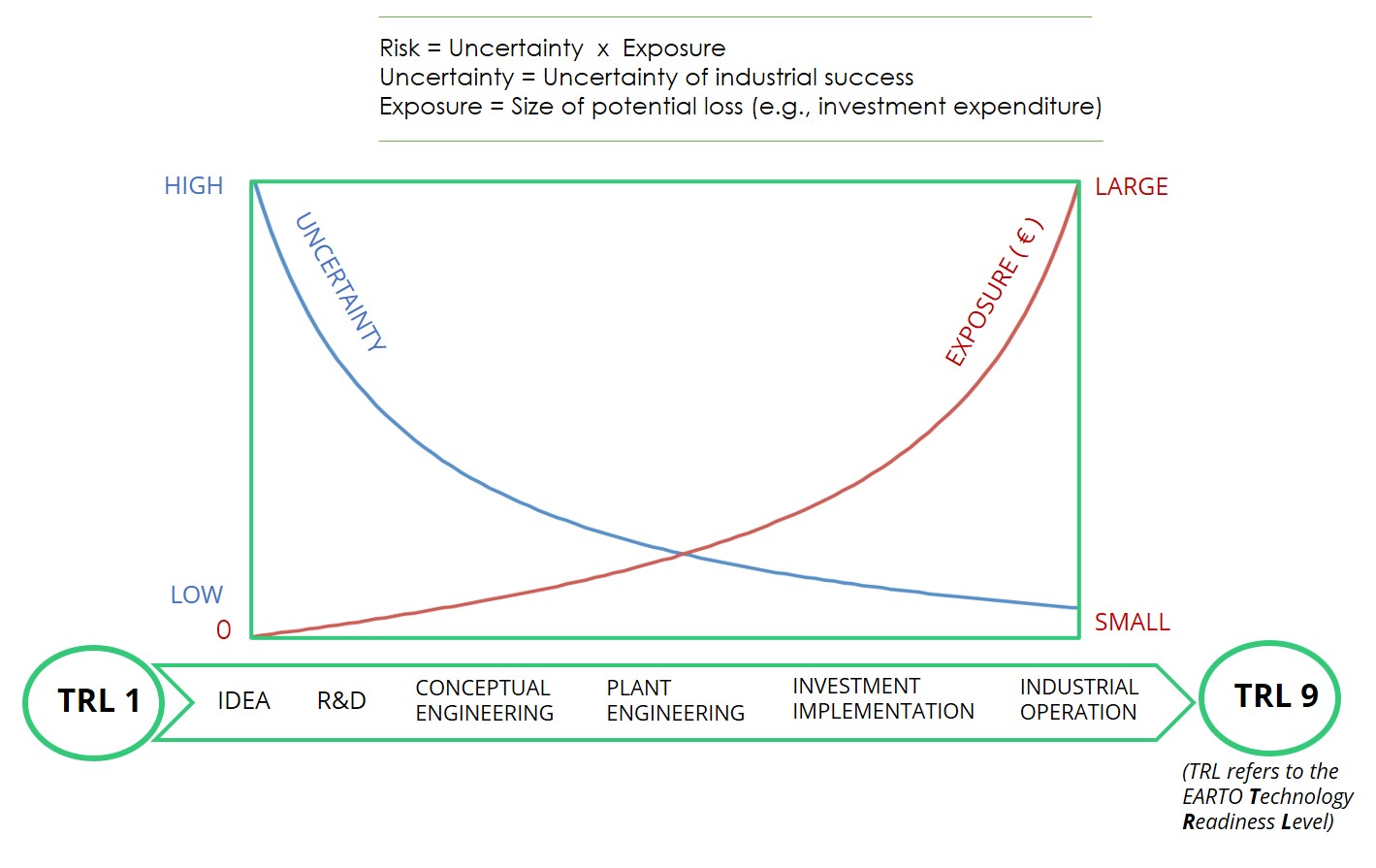
Gaining good, useful insight to industrial technologies in general, and especially when efficient processing of structured plant biomass like wood is in question, requires conscious generation of know-how and understanding. This value-adding process is schematically described in Figure 3. Observations yield data; explaining data yields information and applying information in practice provides know-how. Repeating this process enables gradual build-up of understanding, or increasingly holistic and in-depth insight to complex industrial processes. The purpose of this e-learning environment supports all these exiting steps.
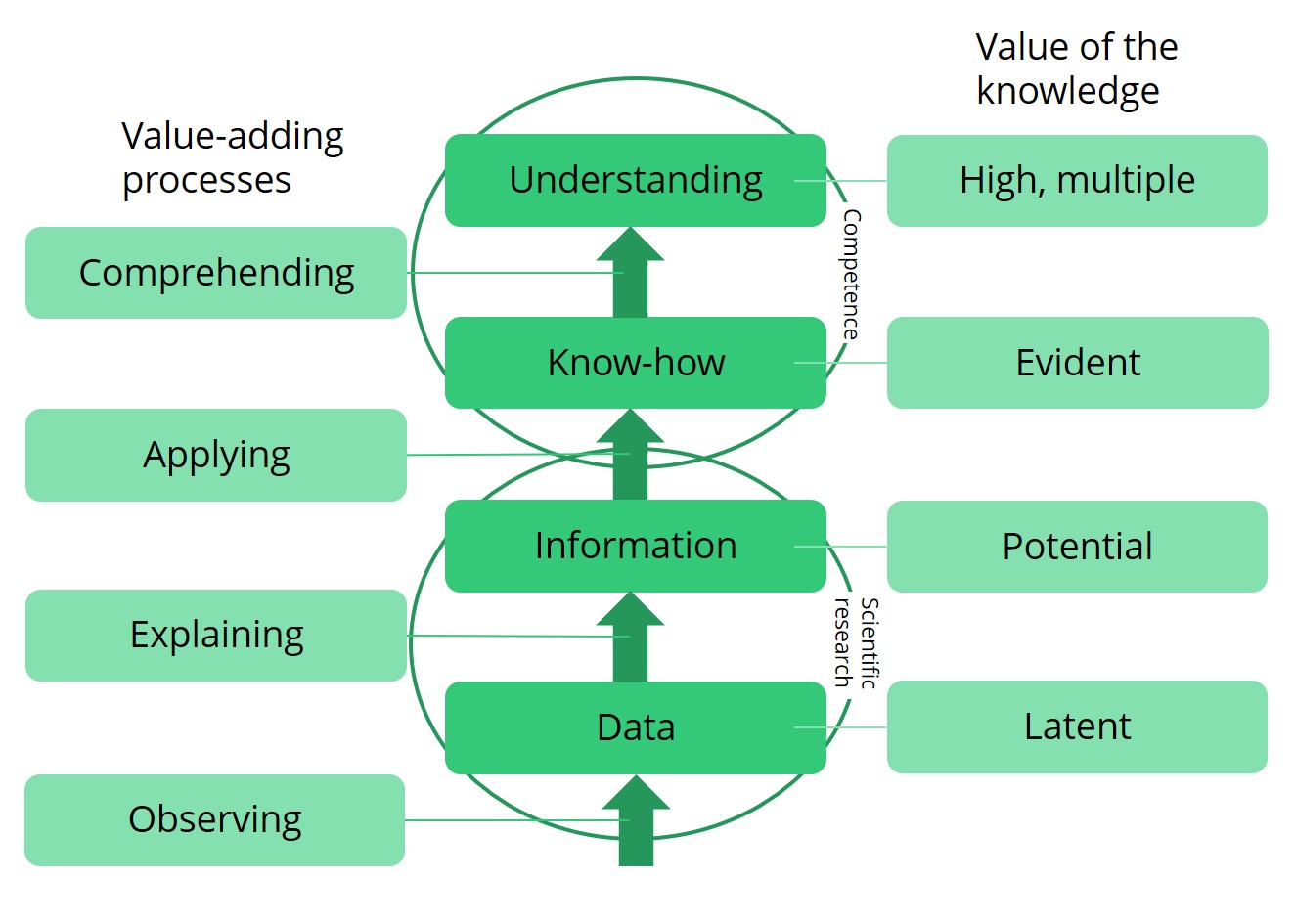
Learn more what CTO Jyrki Ovaska from UPM discusses on the potential of emerging forest-based products.