Jorma Järviö, D.Sc. (Tech), Docent, Service Management Solutions Oy
Asset management
Everything you need to know about the activities and practices to manage company´s assets effectively
To put it simply, asset care means good and efficient ‘housekeeping’ in such fashion that the asset performs its requested function when required. In this way the asset brings return to the purchasing cost. The better the asset functions, the better is the return. Asset management forms the asset care into systematic, planned and manageable form. Asset management is interdisciplinary. One way to introduce the entity is shown in Figure 1.
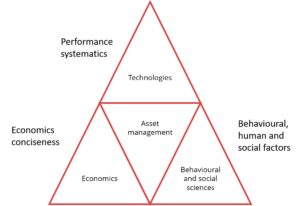
There are 10 sections in this theme:
Introduction – why maintenance?
This section introduces the development of asset management from breakdown repairs to advanced, condition based preventive maintenance. As the machine park of paper mill is not homogenous, different type of maintenance can be applied. Standards are needed when paper mills need to be compared. Standards related to maintenance are introduced in the section. Performance indicators are formed in similar fashion, otherwise the indicators are not comparable. However, use of standards is not mandatory in most cases.
Elements of preventive maintenance
The role of preventive maintenance has become critical. The reason is economical: according to the paper mill case unplanned maintenance costs doubled compared to preventive, planned maintenance. The key to efficient asset management is planning and scheduling of asset care tasks. Measurements show that the work efficiency can even double when unorganised activity becomes organised.
Failure modes
This section introduces information on failure modes. Many equipment defects develop in such fashion that the defect can be observed before equipment stops. Several common root causes of failures are presented in the section.
Total productive maintenance
Total productive maintenance (TPM) is the first large scale program for maintenance efficiency improvement, developed in Japan about half a century ago. TPM is similar to quality programs (plan-do-check-act principle). TPM is a major tool, and it is introduced in seven parts. Overall equipment effectiveness (OEE) method is explained in this section.
Reliability centered maintenance
When the reliability and safety requirement are important, more rigid tools are needed. Most known tool is Reliability-centered maintenance (RCM). Key idea of RCM is that the failures cannot be prevented, but their consequences can. This section discusses failure mechanisms and decision-making diagram.
Asset management and care
Management of assets and care are discussed in this section. Traditional factory maintenance covers all assets that are used in production ‘chain’ or process. The key idea is that the production process (and related costs) can be adjusted to that the yield can be matched with demand of the market.
Maintenance economics
Maintenance economics are introduced in several parts. The problem is higher cost of reactive operation and unreliability costs. These terms are introduced. The way to reach the world-class is not cost cutting but earning most.
Maintenance organisations
In this section different types of maintenance organisation with pros and cons are introduced. There is also outlining of task splitting. EU has launched standards that defines quality requirement for maintenance technicians, supervisor/designer and maintenance manager.
Performance culture
This section introduces the core of asset management ie. performance culture and how it can be created in a company.