Module A5 – Other bio-based materials produced in the forest industry
Introduction
The importance of replacing the fossil-based products with more sustainable bio-based has been increasing and, thus you might be wondering of all the applications and the possibilities bio-based resources have.
This module concentrates on the engineering of biomass into other than wood- or standard pulp-based products. In this module, you will have a general understanding of what man-made bio-based fibre products, polymers and bio-based nanomaterials are and of their end uses and applications.
Bio-based products are not only used in the application of the wood- or standards pulp-based products. These other bio-based products produced in forest industry include:
- Bio-based fibre products
- Bio-based nanomaterials
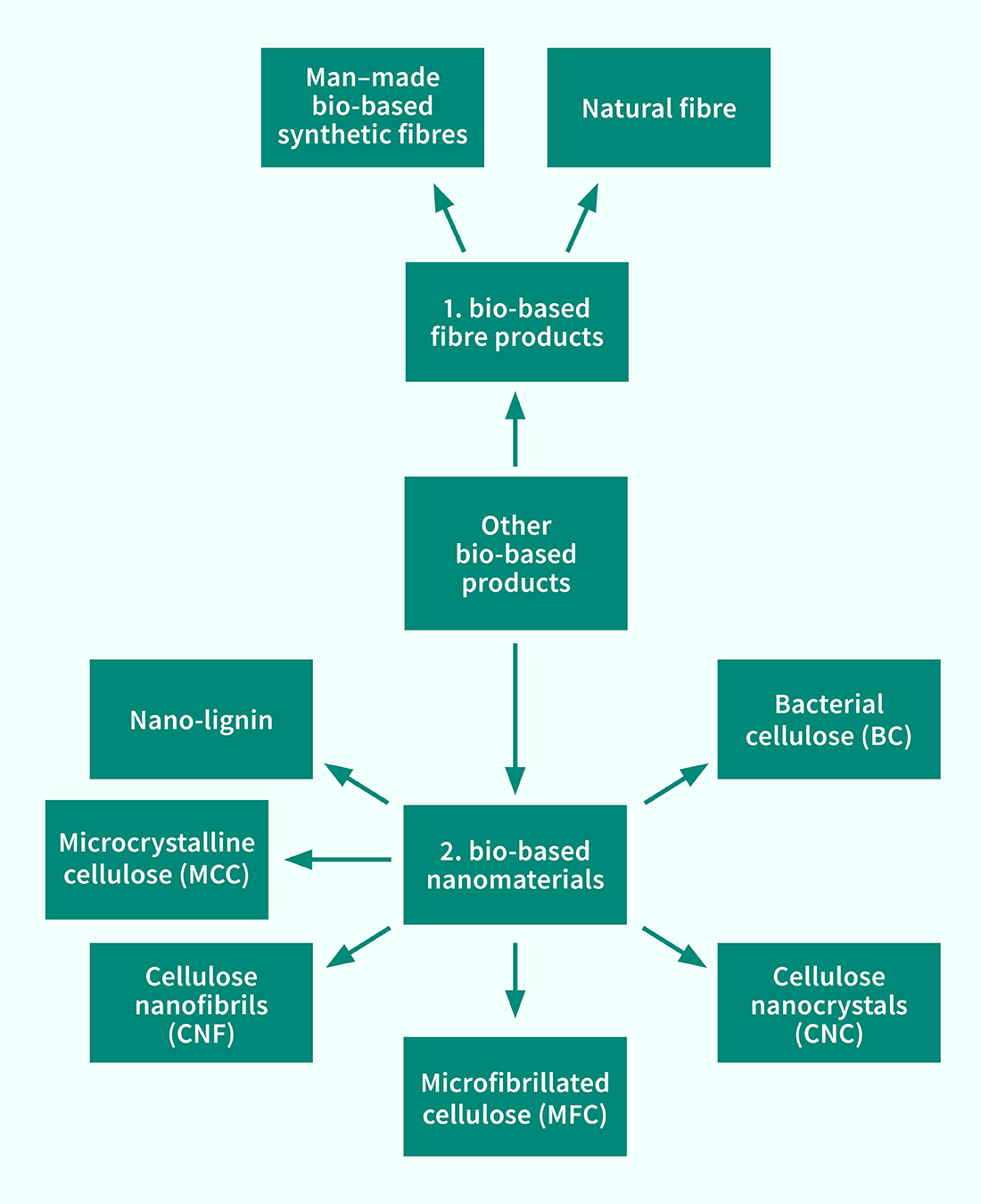
Bio-based fibre products
Man-made bio-based synthetic fibres
Regenerated celluloses are produced by converting natural cellulose to a soluble derivative. Cellulose is dissolved by different methods, after which it can be regenerated in the form of either fibre or film. Viscose, Modal, Lyocell, cellulose acetate, and even carbon fibre can be produced using cellulose as raw material.
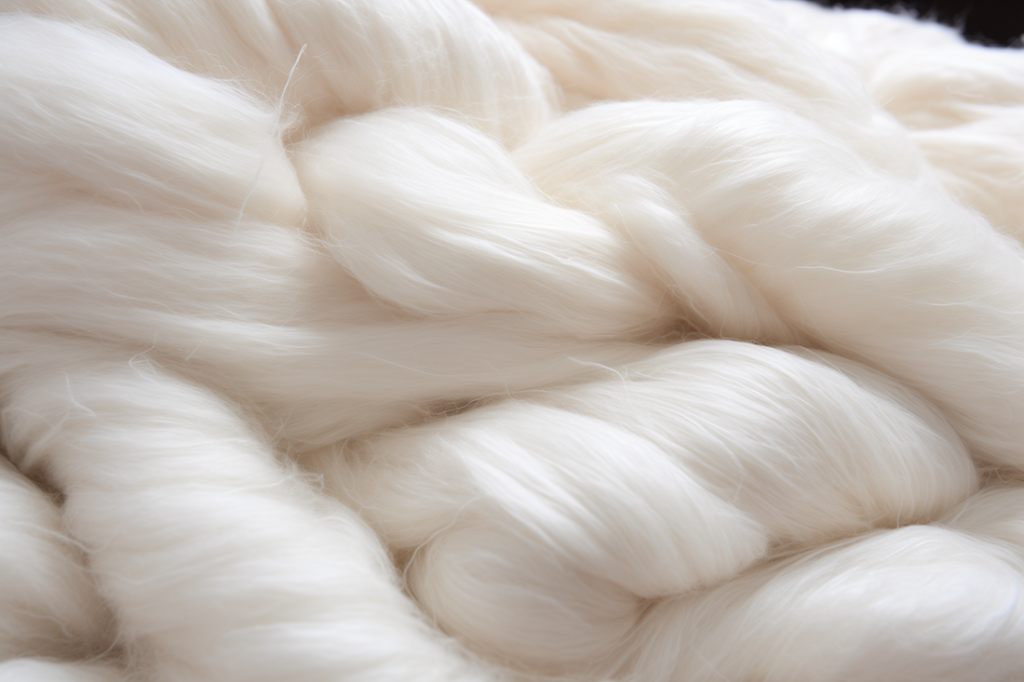
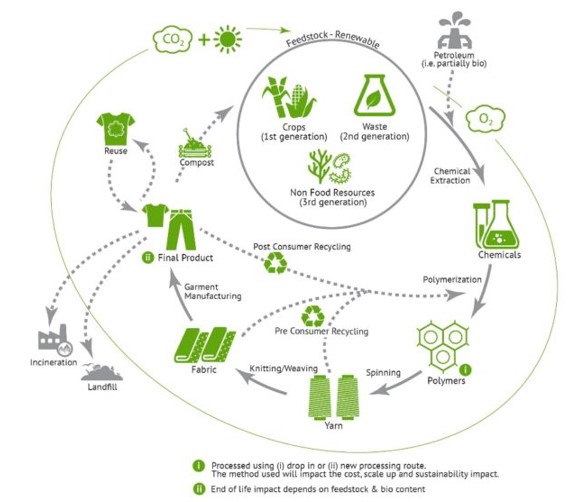
Natural fibres
Natural fibres can be classified based on origin: vegetable-, animal-, or mineral fibre. Another classification is according to their chemical nature. The most dominant natural cellulosic fibre is cotton.
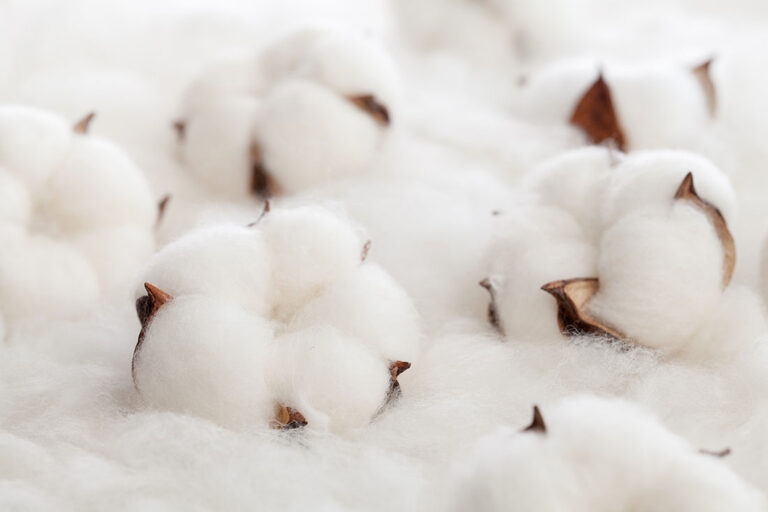
Textile fibres
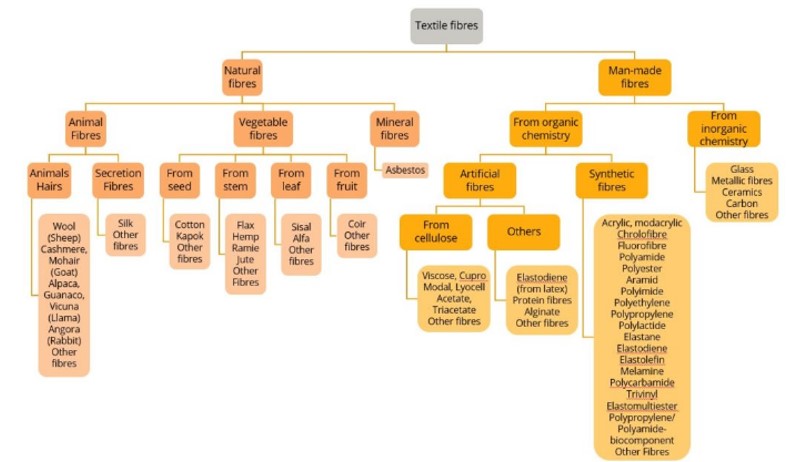
Natural or man-made fibre is used to form basic elements of textile structures (e.g., yarn or fabric). The only requirement of a textile fibre is that it has a certain length and strength, so that it can be processed into textiles
Natural textile fibres are used mainly in clothing and interior textiles where softness, flexibility, absorption of moisture, and possibility to dye are the main characteristics. Some industrial application areas for natural fibres are ropes and twines, packaging materials, and geotextiles.
The textile and garment industry is in a feverish search for raw materials that would provide an alternative to oil-based synthetic fibres and cotton. Renegated fibres made from wood with the help of various technologies represent one such alternative. In contrast to entirely synthetic fibres made from non-renewable oil, fabrics made from cellulose-based fibres breathe, have a pleasant feel to them, absorb moisture efficiently and, above all, are made from a renewable raw material.
Bio-based nanomaterials
Nanomaterials are products that have dimensions in the nanometre scale. They are usually between one to 100 nm in size, and originate from natural, plant-based materials. Cellulose nanomaterials, or nanocellulose (CNF, CNC MFC, MCC), are perhaps the most widely known bio-based nanomaterials, but nano-lignin and nano-sized hemicelluloses have also gained more interest recently.
The potential application range of bio-based nanomaterials ranges from established applications such as strength additives in paper and board, to very innovative ones, such as optical and electronic structures. Their many unique properties give them a great potential as raw materials for novel products in numerous applications
Cellulose nanofibrils and microfibrillated cellulose
Cellulose nanofibrils (CNF) and microfibrillated cellulose (MFC) can be produced from various cellulose-containing raw materials. The fibrillation process is performed by separating the microfibrils contained in the biomass mechanically by grinding, with or without a chemical treatment. Wood pulps are a typical source but various annual plants and industrial side streams, for example from food processing or paper mills, have potential as well.
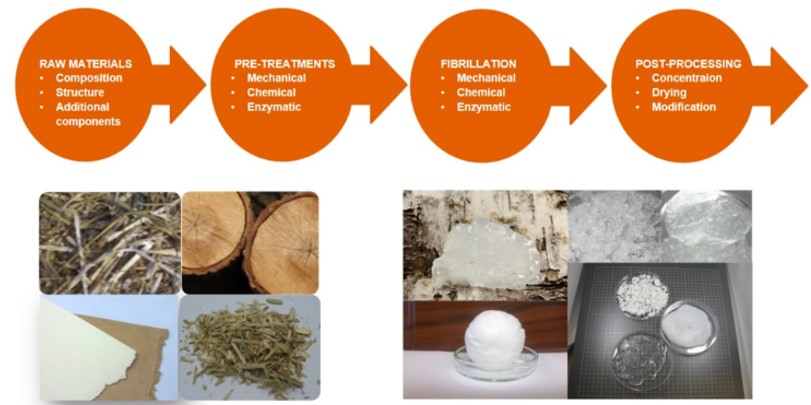
Cellulose nanocrystals (CNC)
Cellulose nanocrystals (CNC) are short, straight, rigid rod-like nanoparticles of highly crystalline cellulose. Cellulose microfibrils are used as raw material, and preparation of cellulose nanocrystals is performed by selective cleavage of cellulose chains in cellulose microfibrils on specific locations, thereby leaving the short crystallites, the CNCs, intact.
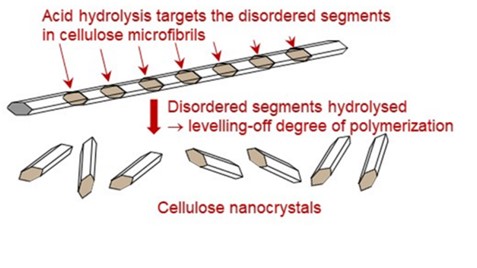
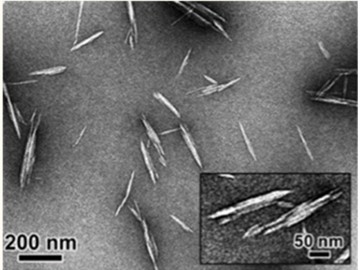
As of 2022, the industrial production of CNCs can still be considered as being in the initial phase, at the early stages of both production and applications. Applications mentioned by entrepreneurs include lubrication, strengthening (composites), blocking (in barrier materials), anti-fogging materials, and viscosity control.
Microcrystalline cellulose
Microcrystalline cellulose (MCC) is, essentially, hydrolysed cellulosic fibres, generally prepared from either wood-based pulp fibres or cotton linters. MCC is currently much more established as a commercial material than nanocellulose grades. MCC finds use especially in the pharmaceutical , food and cosmetics sectors.
Bacterial cellulose (BC)
In addition to terrestrial plants, some bacteria, algae, and animals produce cellulose. Bacterial cellulose synthesis occurs in the cell wall of bacteria, and it is secreted from the cells forming a biofilm as a supportive element.
BC materials have been tested for a wide range of applications due to their unique mechanical properties, including biodegradability, non-toxicity, and biocompatibility.
Nano-lignin
In addition to cellulose nanomaterials, also lignin nanoparticles have recently gained interest. There is a growing demand to find new value-added applications for lignin, and nanoparticles may play a vital role in promoting lignin valorisation. No standardised nomenclature exists so far, but the ones mostly used in the literature are lignin nanoparticles (LNPs), and colloidal lignin particles (CLPs).
Lignin nanoparticles are spherical in shape and can be prepared in many ways. The most common methods work by dissolving wood lignin in an organic solvent, followed by nanoprecipitation of the lignin in an antisolvent which is usually water. This method results in a stable colloidal dispersion of spherical, slightly anionic particles. Another production method is based on aerosol flow, resulting in dry lignin particles.

Colloidal lignin nanoparticles have potential in many applications due to their smooth surface structure and stability in physiological conditions. Examples of applications include cosmetics , household products , building materials , and as an organic filler in nanocomposites.
Bio-based plastics and fibres
The need for bio-based alternatives to replace our current plastics appears obvious. 400 million tonnes of plastics are produced annually – a figure that is expected to triple by 2050 without a global change in direction – and only 15 % of it is recycled. The currently available bioplastic options, made from, for example, corn, sugar cane or waste fats and oils, are still slightly inferior in terms of the performance, mechanical strength and visual characteristics needed for basic packaging material purposes.
Biomass-based polymers could be produced by microorganisms, modified biomass, or biomass-derived monomers. Starch derivatives, cellulose derivatives, hemicellulose- and lignin products can be obtained by processing biomass.
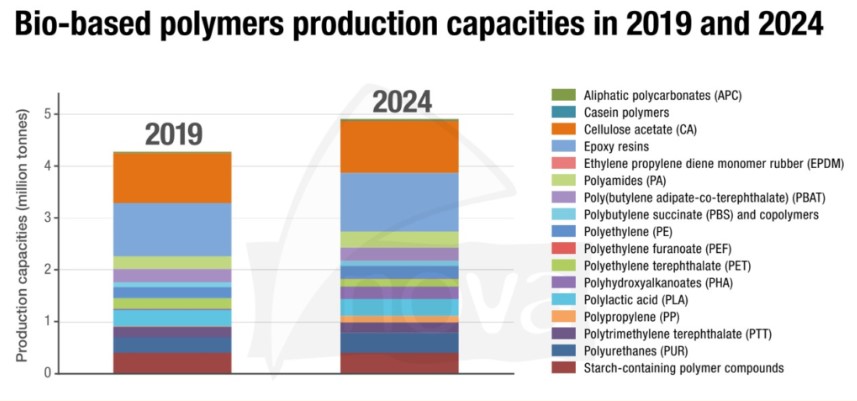