Module A7 – Energy and biofuel production in forest industry
Introduction
Modern pulp mills are turning away from the use of fossil fuels and focusing more on the utilization of biobased fuels. In addition to biofuels, mills are also using recovery methods to produce energy, that would otherwise go to waste.
A state-of-the-art pulp mill is self-sufficient in energy production and even has a considerable amount of power for sale. In integrated pulp and paper mills, the energy self-sufficiency of the mill depends strongly on its production structure.
The energy consumption is highly influenced by the technology employed in the mill. In addition to the technology-specific features, there are also grade-specific or geographically-specific features.Energy costs are 12–17% of the total manufacturing cost and thus they significantly affect the profitability. The share of energy cost in pulp and paper manufacture is three to four times higher than in the manufacturing of the wood product industry.
In this module, you will learn more about these different recovery processes and other sustainable ways the forest industries generate heat and power.
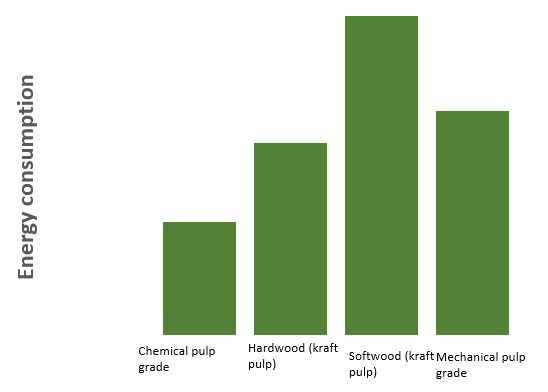
Production processes recovery and energy
The forest industry consists of the mechanical forest industry and the pulp and paper industry. The pulp and paper industry includes the production of pulp, as well as paper and paper board production. The main energy consumer and producer in the pulp and paper industry is chemical pulp manufacture.
In chemical pulp manufacturing process, the weak black liquor is separated from the pulp by washing, and is sent to the kraft recovery system, where the inorganic pulping chemical are recovered for reuse and the dissolved organic compounds serve as a fuel to produce steam, which is used to generate electricity.
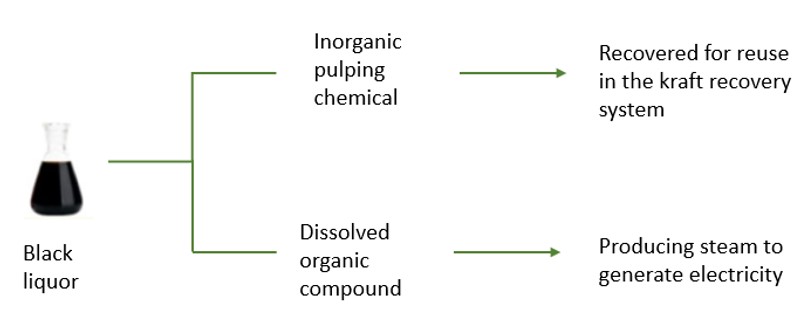
The recovery process
Weak black liquor is concentrated in evaporators and concentrators to a point where it can be effectively burned in a recovery boiler. The process has three main functions:
- recycling used pulping chemicals back into usable forms, NaOH and Na2S; and
- co-generating steam and power though burning the organics and
- minimising the environmental impact of black liquor combustion and other side streams formed in the pulping process.
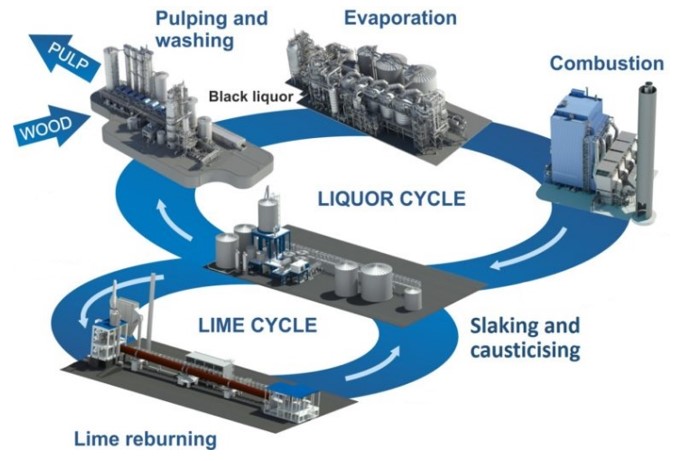
Evaporation
In evaporation process, the water is removed from black liquor. The other purpose is to separate methanol, turpentine and soap, which are generated in the cooking phase. The evaporation is done in evaporators where the dry solids content of the weak black liquor is increased to form strong black liquor.
Heat and power generation
Energy is produced using two different types of boilers:
- Recovery boiler
- Biomass boiler
Recovery boiler
Recovery boilers are used to burn organic residue from chemical pulp manufacture. The recovery boiler has the following purposes:
- to recover cooking chemicals in the black liquor
- to produce energy for the pulp mill by burning organic material in the black liquor
- to get rid of odorous gases generated in the pulping process.
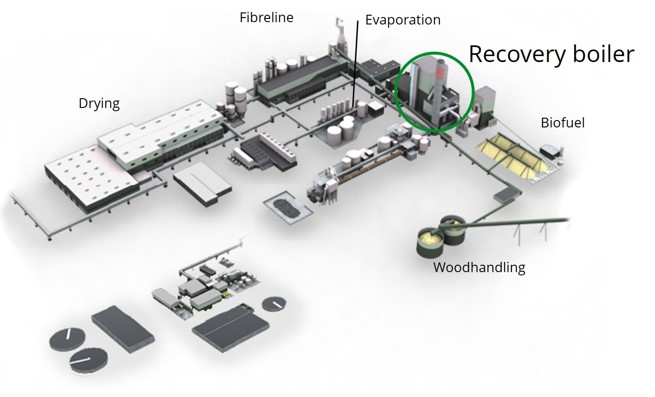
Biomass boiler
Residues and bark are typically burned in biomass boilers. The heat stored in wood is released in combustion reactions in the furnace. The biomass boiler has the following purposes:
- to recover heat from combustion and to generate steam
- to convert steam for electricity and heating purposes
- to generate steam during mill shutdowns
- to contribute to district heating systems
The heat that is obtained in combustion is recovered in the biomass boiler to generate steam. Steam is converted to electricity in the turbine or it is used for heating purposes. The biomass boiler is also used to generate steam during mill shutdown and for additional needs like papermaking, other processes, and district heat.
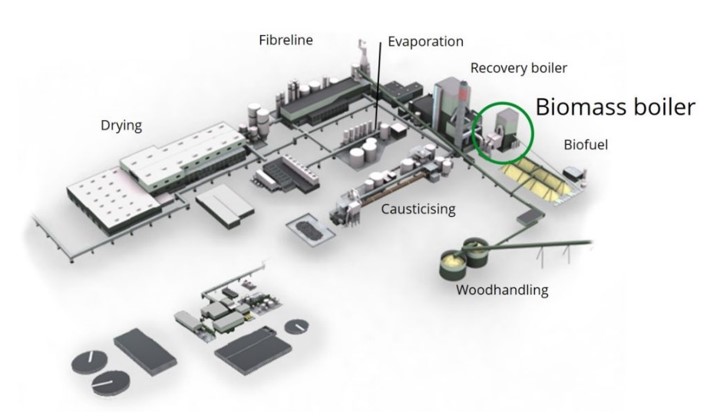
Heat recovery for increased energy efficiency
Heat recovery is a process where heat from warm water or gas is collected and re-used from boilers that would normally be lost. Gas is recovered in the combustion of fuels in the recovery boiler of a pulp mill for increased power production. You can go to Learning path B, chapter 11, if you are interested in learning more about fuel gas recovery process.
There are alternative ways of utilising the heat available in the flue gases. The fuel gas recovery can be:
- condensing fuel gas heat recovery:
where there is a direct heat exchange to the target media (e.g. flue gas heats water).
- non-condensing fuel gas heat recovery:
The heating is done with direct heat exchange to target media (e.g., to combustion air or hot water) or indirect connection, using typically water as the heat transfer media
Novel solutions in the pulp mill energy supply
High volumes of wood residues such as bark and fines are generated in the pulp mills and currently combusted to produce heat. Alternatively, the residues could be pelletised for external use or processed via other thermo-chemical reactions for further upgrading.
The black liquor can provide an extensive platform for producing biofuels. Examples include extracted lignin as a precursor to biocrude oil, gasification to produce dimethyl ether (DME) and processing of tall oil to produce biofuels for transportation. Electrolysis and CO2 capture are new options that will be important in the new pulp mills.
If you want to learn more about the other novel energy production methods, press here.
Biomass gasification
Production of extra electricity and the high unit cost of recovery boilers are the main driving forces for the development of gasification. From an energy efficiency standpoint, the recovery boiler has several weaknesses; the main steam temperature and pressure are low, the energy in smelt is not recovered and the combustion temperature is only moderate.
Gasification provides a way to convert solid fuel into gases. Energy conversion always involves exergy and energy losses. Gaseous fuel enables the use of combined cycle power generation, where both gas turbine and steam processes produce electricity. This increases energy efficiency. Higher yields of biofuel-based electricity fits with national and international targets and reduces production of fossil CO2.
Improvement of energy efficiency
Production efficiency is the key to improving energy efficiency. The energy efficiency of forest industry processes can be improved by:
- new modes of operation
- improvement of skills and motivation of personnel
- energy audits
- enhanced process integration of existing processes and industrial plants
- collecting of reliable process information (monitoring and control)
- modern financing mechanisms of energy conservation projects (ESCOs)
- introduction of more energy-efficient technologies
- electrical devices with low energy consumption (motors, pumps etc.)
The efficiency of energy consumption (as well as energy production) of existing mills can be improved by utilising the BAT techniques.