Module A6 – Making of pulp, paper and paperboard
Introduction
Have you ever considered how your morning newspaper or the copy paper that comes from the printing machine has been manufactured? Have you ever been intrigued to learn more about the background of paper and paperboard? In this module, you will get to learn how the production from wood to pulp, paper and paperboard happens.
The production of pulp, paper and paperboard has evolved throughout the years, and it has become more sustainable by using more environmentally friendly and bio-based raw materials. For instance, more companies are utilizing the by-products from the production processes.
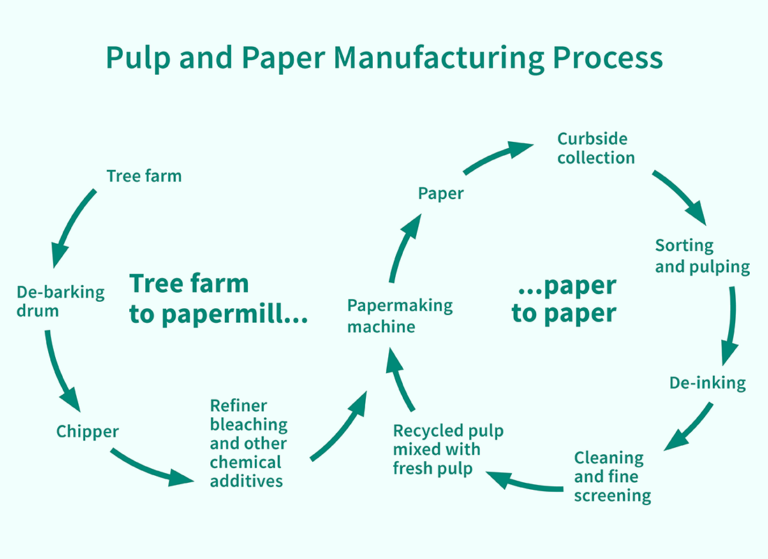
Making pulp
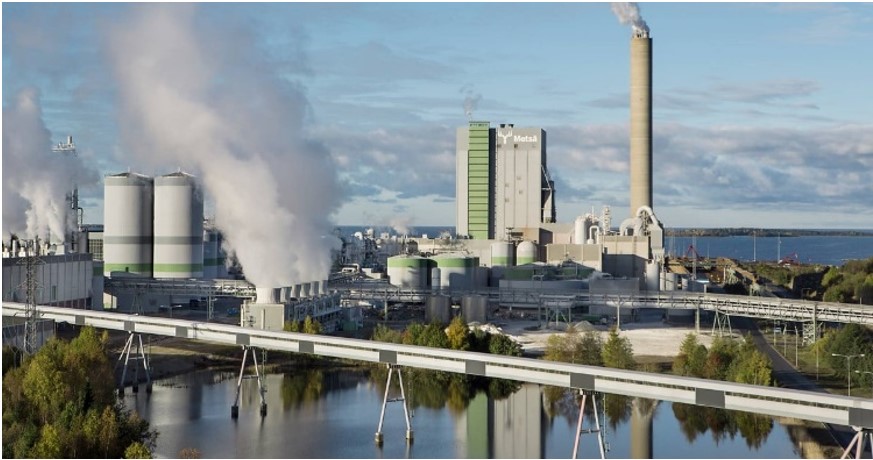
Wood and other fibrous materials are processed in many ways to produce pulp as a raw material for paper- and paperboard production. Different fibre separating methods are collectively called pulping processes and can be performed either by applying:
- mechanical grinding forces to woody masses (i.e. mechanical pulp)
- chemical processes (i.e. chemical pulp)
- Recycled pulp processes
Additionally, the use of recycled pulp in the production of paper and paperboard is also possible. Approximately 7% of the fibre material used in the Finnish paper and cardboard industry is recycled pulp meanwhile the average use of recycled pulp in other countries in the Europe is around 50%.
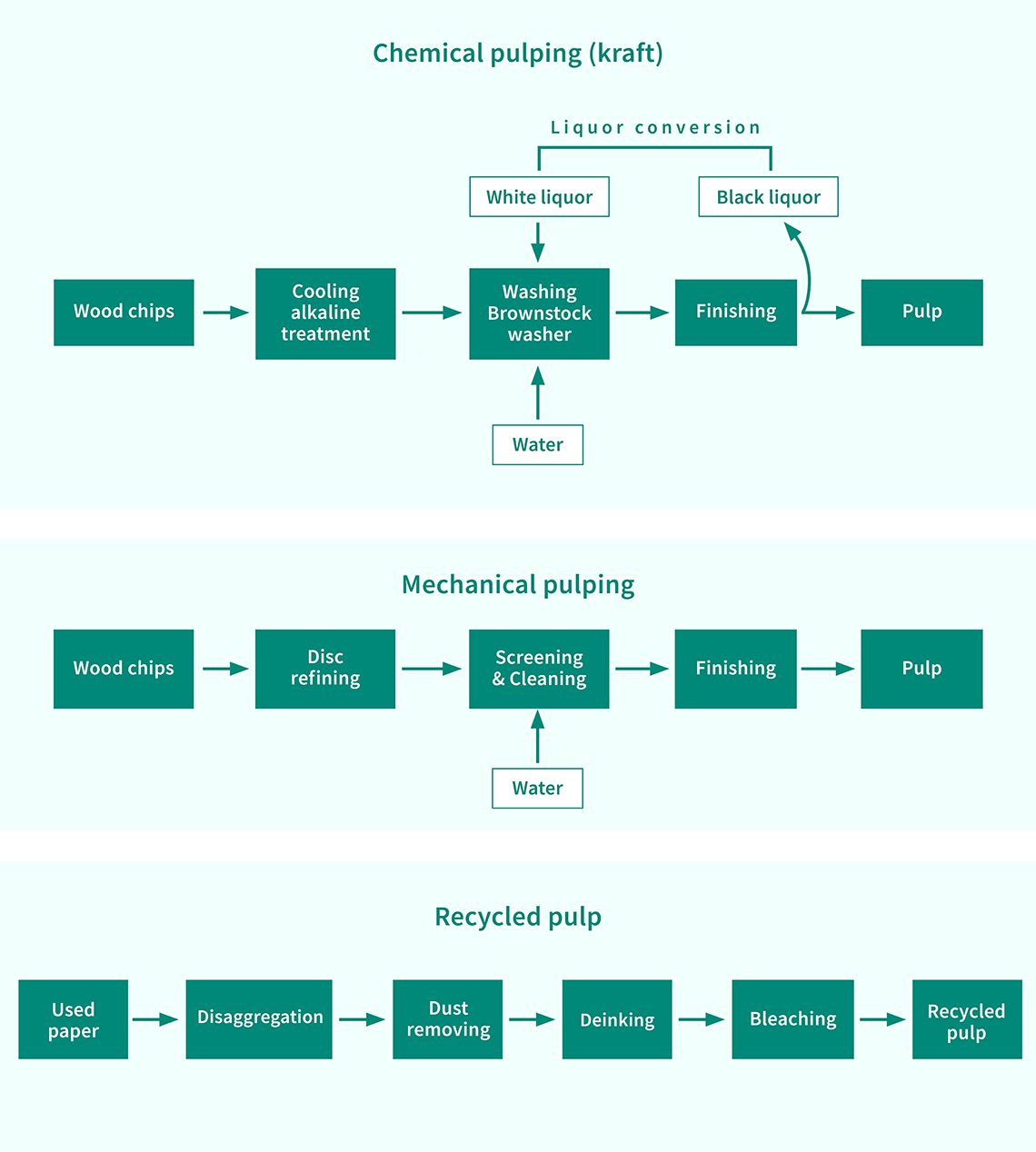
Chemical pulping (kraft)
Kraft pulping is the overall naming for chemical processes, where wood chips are cooked at elevated pressure and temperature in white liquor. Kraft (sulphate ) or sulphite processes are used in cooking. The dominant kraft pulp can be made using softwood and hardwood as raw material, whereas the conventional acid sulphite pulp is principally made using only spruce as raw material.
Lignin is a coloured substance that binds the cellulose fibres together. It is degraded and softened in the cooking process and can be washed away, making it easy to separate individual fibres from each other. Pulp has a dark brown colour after cooking and is bleached with different methods if needed. Bleached chemical pulp is used in high quality wood-free printing papers and packaging materials that require a good visual appearance combined with strength properties. Chemical softwood pulps contain long, practically undamaged fibres which provide excellent strength properties to paper and paperboard
Fibre material used to be the only material of interest, however the development of new products from the side streams (e.g. lignin, ash) of pulp production has increased exponentially. For instance, Stora Enso has manufactured NeoLigno, natural lignin-based binder. Another example of utilizing by-products is Metsä Group using ash as a fertilizer.
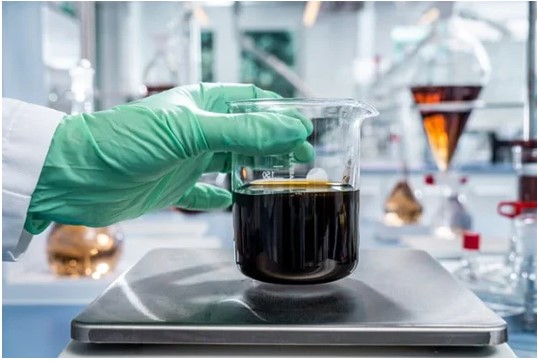
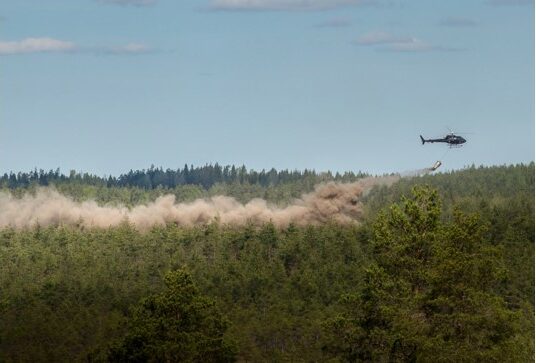
Mechanical pulp
Three basic technologies are used in producing mechanical pulp:
- Groundwood pulp (GW, SGW) is produced by pressing debarked wood logs against rotating grindstones with a ceramic grit surface to detach fibre from the surface of the logs. Spruce softwood is used.
- Thermomechanical pulp (TMP) is produced by heating cut wood chips with steam before refining between grooved steel grinding discs. Spruce softwood is used.
- Chemithermomechanical pulp (CTMP, BCTMP) is produced by softening wood chips with impregnating chemicals and steam to ease the fibre separation during refining. Softwood and hardwood can be used.
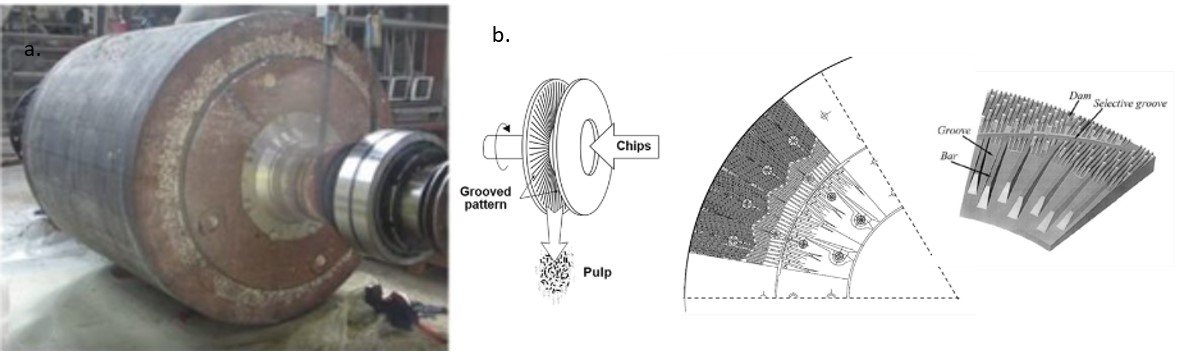
Recycled pulps
In general, paper and board are easily re-usable after their manufacture. Recycling describes the reuse of paper for recycling within the paper and board industry to manufacture new paper and board grades.
For all paper recycling processes, it is essential that the paper products can be disintegrated. The recycled pulp is obtained via disintegration process. It is carried out by using water, releasing the fibres. Paper for recycling is relatively easily repulpable in aqueous conditions by applying sufficient mechanical energy.
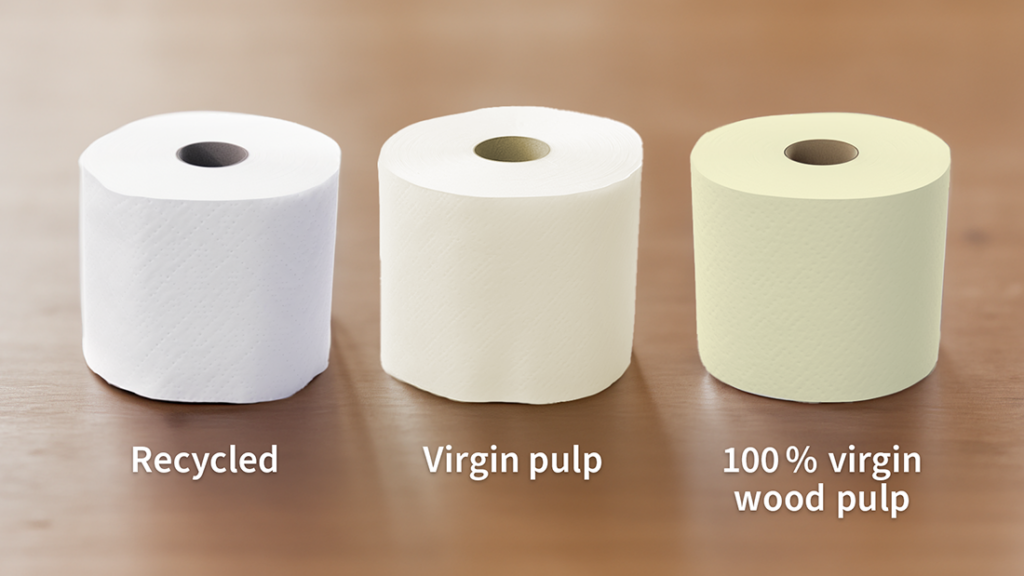
As recycled pulp is made from used paper, to produce white and clean pulps, inks and toners have to be removed. The deinking process has become one of the key technologies of paper to be used in recycling treatment plants for the production of graphic papers, sanitary papers and even white top plies of testliner or board. Watch the video below on how pulp is made by UPM.
Making paper and paperboard
Paper and board machines run at steady state with maximal operation rates, producing homogenous paper or board quality according to strict product specifications asserted by customers.
The papermaking process steps include: stock preparation, short circulation, headbox, water removal (incl. web forming, wet pressing, drying), and lastly finishing of the paper.
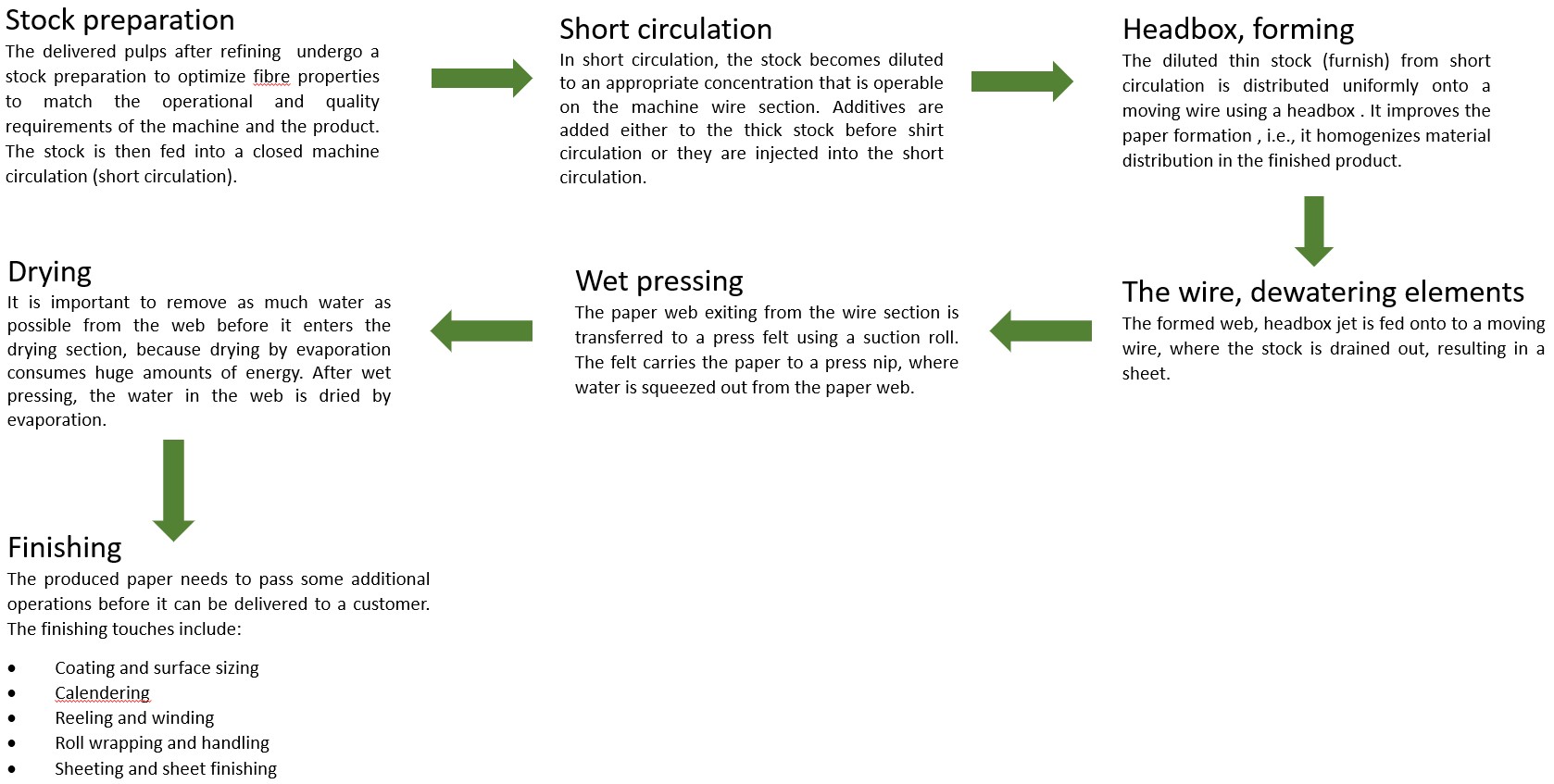
Finishing
Coating and surface sizing
In the coating process, coating colour is applied to one or both sides of the paper or board. Coating increases the smoothness of paper considerably. After application, the desired amount of coating material is metered and dried.
In surface sizing, typically a starch-based sizing agent is used to mainly improve the strength properties of paper and board surfaces before coating.
Calendering
In calendering, the web is passed through a nip between two or multiple hard rolls generating a combination of mechanical force, heat and moisture which smoothens out and planes the paper. Calendering increases the paper gloss and improves the printing and coating performance of a paper.
Reeling and winding
The process from headbox to reel is continuous. Paper becomes rolled to large diameter and cut to narrower rolls or sheets and stacked for packaging based on the customer’s needs.
Roll wrapping and handling
The paper reel is packaged to protect the product against mechanical wear, tear, moisture and dirt during transportation and storage operations. Modern roll packaging lines are fully automated. The system typically also includes systems that provide the roll either with wrapping or strapping and can also be connected to warehouse operations like storage management and shipping.
Sheet finishing and packaging
Sheet finishing and packaging is performed according to the same criteria as the reels. Pre-trimmed reels are cut into sheets with well-defined sizes and packed.
Virtual papermaking tour
Welcome to the virtual papermaking tour! In the video below, you can learn more about the papermaking, what the main processes are, listen to interviews by operations’ professionals and also take a 360 degrees virtual visit by the paper machine (VR headset required). The material has been produced in close cooperation with Sappi Finland’s Kirkniemi Mill.