Module B14 – Process maintenance and asset management
Key source in ForestBioFacts: Asset management – ForestBioFacts
Learning targets
This article talks about the important role of maintenance, preventive maintenance, and failure modes as well as asset management and care. Maintenance economics and organisations are also discussed.
After reading this article you will have received insight into…
- why maintenance is needed
- elements of preventive maintenance
- asset management and care
- maintenance economics
- maintenance organisations
- performance culture
Introduction
To put it simply, asset care means good and efficient ‘housekeeping’ in such fashion that the asset performs its requested function when required. In this way, the asset brings return to the purchasing cost. The better the asset functions, the better is the return. Asset management forms the asset care into a systematic, planned, and manageable form. Asset management is interdisciplinary. One way to introduce the entity is shown in Figure 11.
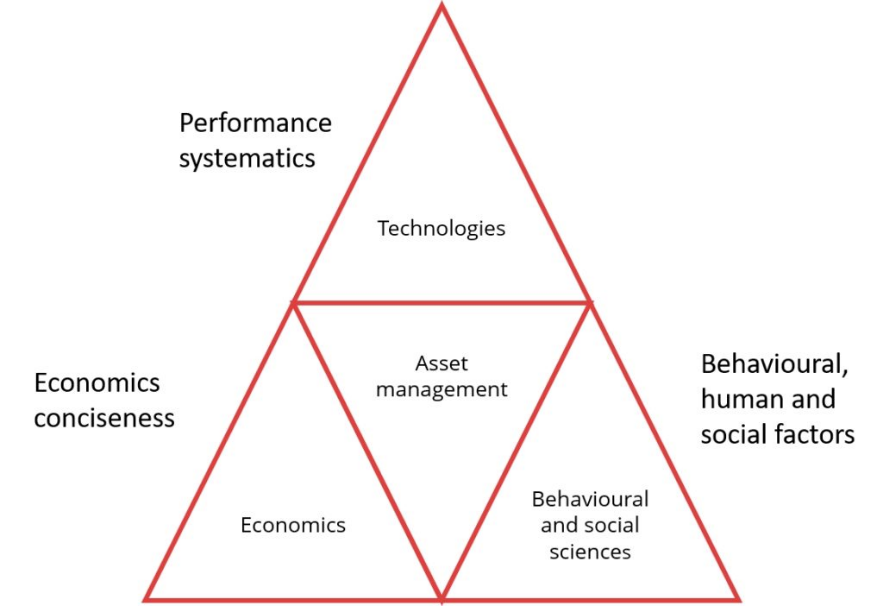
Why maintenance?
Plant machinery and equipment eventually wear out. Asset management from breakdown repairs to advanced, condition-based preventive maintenance are needed to keep machines and instrumentation in good working condition 1.
Maintenance is an effective way to keep plant machinery and equipment in good working condition during their lifetime, and an effective measure to ensure their reliability. Inadequate maintenance results in equipment failure, consequently poor product quality and process reliability, higher process and operation costs, and may influence the safety and health of workers. Lack of adequate maintenance may lead to unexpected plant shutdowns, tragic accidents, and costly losses 1.
Asset management
Key source: Introduction – why maintenance? – ForestBioFacts
All resources owned by a company and used to produce value are referred to by the term ‘asset’. Plant equipment and machinery are a company’s physical assets and in capital intensive industries such as chemical or pulp and paper industries they represent the most important share of the company’s investments. Effective management of physical assets such as plant equipment and machinery include both economical aspects and maintenance 1.
In large-scale process industries, the cost of a breakdown/stoppage is considerably higher than keeping the process in good condition. The best approach is to detect and correct the problems before defects stop the process. Good asset care requires performance culture known also as efficiency culture. It is like the driving force of a team willing to win. Recent measurements show that the reliability of machines depends more on operation than maintenance. An old belief that the maintenance department is solely responsible for the runnability of the asset is wrong 1. Also, maintenance expenses are normally considered as costs for a company. On the contrary, they should be considered as a part of company’s investment 1.
The reliability of the company’s operations is a critical success factor (CSF) today. Maintenance is one of the most significant key success factors for a company. A company with effective maintenance management gets higher return of investment (ROI). Efficient production and high utilisation, increased profit and strong cash flow, occupational safety and environment-friendly operation are among the benefits of preventive maintenance for a company. The impact of proper maintenance results also in a stronger balance sheet: increased plant lifetime (smaller tax write-offs), improved plant asset management, increased capital turnover and reduced overall operating costs 1.
Maintenance practices
Total Productive Maintenance (TPM) focuses not only on manufacturing and maintenance, but also on the whole production environment and process, its efficiency, economy and ‘goodness’ (integrity, precision). It also includes environmental and safety aspects.
TPM improves productivity and reliability and reduces waste and aims to continually improve all elements of the operational process (cooperation between man and machine). The goal of TPM is Zero Breakdowns and efficient use of materials and energy as well as the avoidance of errors and unnecessary work. Its characteristics include ‘owning’ the means of production and taking responsibility (everyone checks and manages their own ‘environment’), the positive participation of all, and willingness to improve. TPM aims to influence a company’s culture by making everyone, regardless of their position, strive to be the best and make the operation effective. Because the TPM concept has proven to be successful, the programme has been refined as a consultant tool 1.
Maintenance as a service
Maintenance can be done by an internal maintenance department (also known as in-house maintenance) or alternatively by an external service provider, for example, by an equipment provider or an independent maintenance company. Outsourced maintenance is becoming an increasingly common way for companies to maintain their assets. Outsourcing has had a positive impact on the maintenance business: increased competition has improved the quality of maintenance services provided by companies 1.
Maintenance culture
Improving performance requires the construction of a company’s operating culture in such a way that all business functions work for a positive result. Everyone wants changes that will lead to something better. The maintenance department cannot assume sole responsibility for reliable operations. This is mainly the task of the equipment operators. Accountability is possible when the company management takes the role of a clear and active leader in the development of the processes.
Maintenance is often focused on reducing costs. There are three ways to do this 1:
- Working more efficiently – this is the best way to reduce costs. Key factors for more efficient working include verification, prioritisation, task planning, scheduling, implementation, analysis of results, and improvement of performance. By making things right, we can develop best practice actions. This approach is company-specific and must be developed by company management.
- Reducing maintenance needs requires discontinuation of old patterns of action. First, it should be decided what a company wants, and then how this goal can be achieved. Often, help can be found in the condition monitoring, by means of which a company can avoid unnecessary checks and carry out corrective action on a need’s basis.
- Taking maintenance debt (= do later) is possible, but there are unpredictable risks. It is often forgotten that the maintenance debt has interest, in fact compound interest (interest on interest). For example, if a hundred tasks are to be postponed for the next period, the new workload is equal to debt plus interest. We all know that in case repairs are not done in time, failure development will accelerate. The savings that have been achieved entail multiple costs. If this happens too often, the payback becomes too expensive; and there simply is not enough money.
Fourth generation
Maintenance is transforming from reactive breakdown repairs to managing production assets. Four generations can be distinguished in this development between 1940–2010 3. Maintenance generations – ForestBioFacts.
The characteristics of the first generation:
- inoperative machines were kept idle (low integration, various parallel production lines),
- production machines were quite simple, the most common mechanism of machine failure was time-related failure, but without the infant mortality
- machines were over dimensioned (inaccurate design and calculation methods were compensated by generous safety factors)
- failure finding, localisation was easy
- proactive maintenance consisted mainly of adjustment, cleaning and lubrication. The required skill level for maintenance crew was relatively low.
… …
Currently, the fourth generation takes note of the following issues:
- Maintenance is no longer limited to mechanical equipment; it also includes the maintenance of programs that control the functions of the equipment.
- Smart sensors can be used for measurement of items that was previously not possible (toxic environment, temperatures in furnace). Sensors can transmit data to the maintenance operator (e.g., IoT applications).
- The quality of the operation can be measured indirectly by measuring the end-product or manufacturing process.
- Computer technologies have developed devices that allow for varying degrees of monitoring (monitors in control room). Processors that operate/control the process can also control operating conditions and quality of use. Data is stored (data warehousing) and analysed (data mining). This information can be used to perform an accurate root cause analysis and follow up on the ageing of the device (lifetime analysis, determination of the remaining safe life span).
- Remote monitoring (e.g., IoT makes it easier to use resources and allows experts to be used more effectively.
- The reliability of the item can be monitored. When sensors (or other tracking data) indicate that the data is not what it should be, the logic will assume that there is a defect and trigger action to determine and correct the cause. In this way, condition monitoring becomes more based on actual data. Condition monitoring tasks can increasingly be carried out by the machine operators.
- New factors such as the quality of products and operations, safety, and protection of the environment are emerging in maintenance.
- Maintenance is a way of adjusting the operating efficiency of machinery. This offer means to compensate for fluctuations in demand 4.
Maintenance types
The division of the manufacturing activities into different types is a prerequisite for effective maintenance management and control. The maintenance types are the tools making it possible, for example, to monitor the efficiency of maintenance by comparing the cost of different types of work, the number of hours worked and results 1.
The main types of maintenance are presented in Figure 2. Note that the material is adapted; for more detailed information, please check the original standard noted in the picture capture.
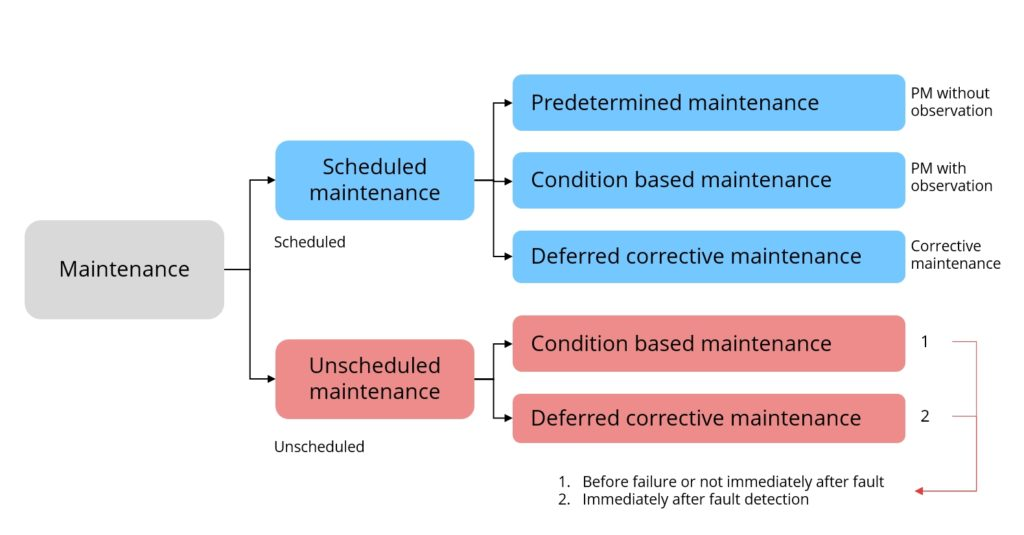
Another way to divide the maintenance types is presented in the local standard PSK 6201:2011. It divides the maintenance types based on whether they are planned or performed due to the production disruption. The division is shown in Figure 3.
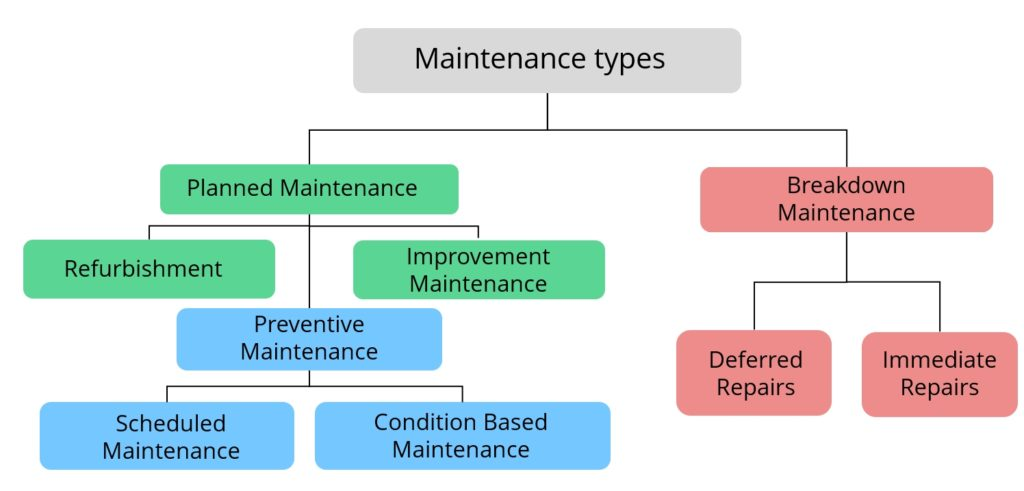
Planned actions are executed before the failure has stopped the required function. Failure requiring breakdown maintenance will result in a breakdown state (production break). Repair can be deferred, if reasonable, to minimise logistical and/or administrative delays.
Asset care – maintenance types
John Moubray introduced a new maintenance type that he called analytical maintenance. It includes actions and approaches that deal with root cause finding and similar ‘detective’ tasks that aim to eliminate failures directly or indirectly, improve quality and the utilisation of an asset through maintenance. These actions include failure/fault analysis, failure detection and simulation, modelling, and reconstruction, RCFA, LTA, materials and design analysis, and risk management. Figure 4 shows the traditional approach that is still widely used today.
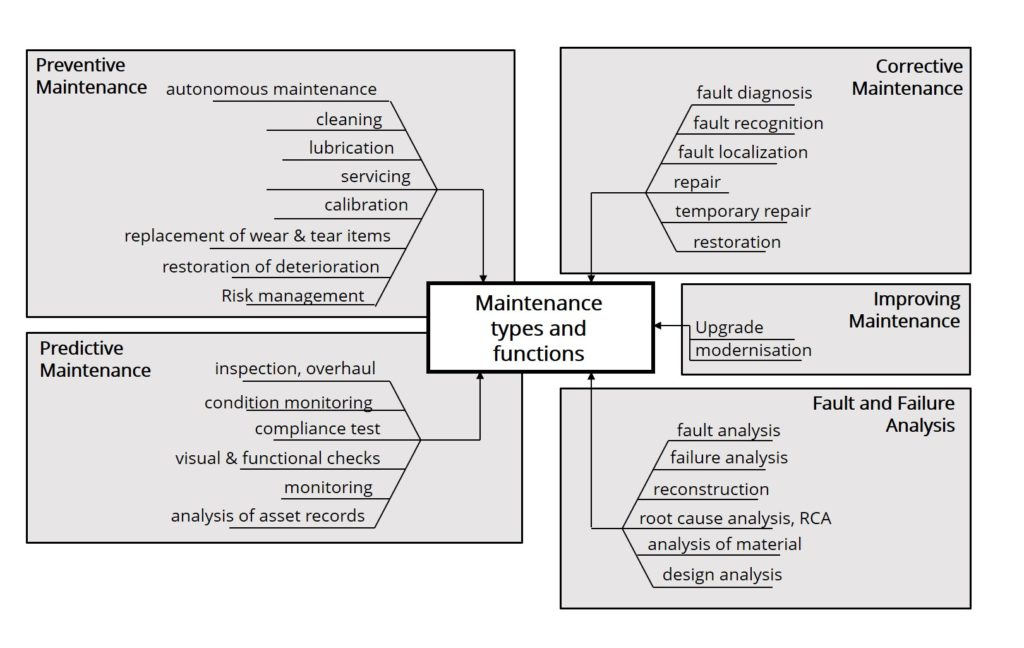
Service is a pre-determined maintenance activity including item check-up, adjustment, cleaning, greasing, oil change, filter change and other corresponding activities. The aim of service is to maintain an asset’s operating characteristics or restoring impaired performance prior to failure or to prevent damage. Systematic (planned and scheduled) service is performed at intervals.
The basic idea of preventive maintenance is to monitor the performance of the machine. The goal is to reduce the likelihood of failure or decrease in the operating capacity of the machine/component. Preventive maintenance is regular (scheduled or continuous) or is performed on demand. The results can be used to plan and schedule maintenance tasks.
Corrective maintenance means restoring failing or failed components. Corrective maintenance performance dates and times can be used to calculate the lifetime of a component. Corrective maintenance is either unplanned or deferred. Process shutdown is inevitable.
Improvement maintenance can be divided into three main categories:
- An item is changed using newer elements or components than the originals, but the performance of the item is not actually changed.
- A variety of redesign and corrections to improve a machine’s unreliability. The purpose is to change the operation of a machine to be more reliable rather than to change the performance. Example: the engines of a commercial airplane are replaced with more fuel-efficient types. Now the plane can fly without a fuel stop from Europe to the Far East.
- Modernisations in which the performance of a machine is changed. In general, modernisation is done to the whole manufacturing process. For example, if a paper machine’s life cycle is not over, it makes more sense to modernise it rather than to abandon it to buy a new replacement.
Large modernisations require a lot of design work but are considered as an investment and therefore not considered to be maintenance. When used as a concept for the management of production assets, the view changes 1.
Identifying faults and failures
Defects and failure detection have not yet been treated as a maintenance activity. Their importance is understood, and today more and more maintenance organisations are using root cause methods (and software) as an everyday tool.
Modern production machines have a very large number of operating processors, which also collect information on the operating, load, and operating conditions of the machine. This information is easily available for the analysis of the root causes. Once identified, it is possible to plan and take corrective action that will have a radical impact on the reliability and performance of the machine. It is normal to wait for the failure to be reduced by up to more than 90% when healing ‘maintenance troublemakers’ 1.
Maintenance standards
The use of uniform concepts is essential for the unambiguous presentation of things. Earlier, when businesses were in the growing phase, even the comparison of corporate financial data was difficult because every company, for example, calculated its results differently. Acquisitions and mergers were laborious. Additionally, there has been direct misconduct on the economic side, which has deliberately miscalculated the company’s key figures in a more favourable light. However, legislation has changed and today the misrepresentation of key figures (especially economic figures) is a criminal activity. The same applies to the management of production assets. Communications and research reports become difficult unless the terms and concepts as well as their use are unambiguous 1. (Link: Maintenance standards – ForestBioFacts)
Elements of preventive maintenance
Preventive maintenance (PM) plays an important role in the performance of the enterprise. The easier task is to identify failures and fix them before the assets shut down. The more difficult task is to eliminate root causes and thus prevent failures. Efficient PM requires active participation from asset operators and maintenance crews.
By means of PM, the reliability of processes can be completely assured. Breakdowns are unavoidable, but their consequences can be avoided through RCM 1.
Recent legislative developments regarding safety and environmental risks have become stricter. If such a risk occurs, the management of the company will have to respond to the authorities. In several countries, the management cannot hide behind unawareness. If management is not aware of the legislation, they must obtain these particulars. Unawareness today is a criminal act 1.
The effective preventive maintenance consists of the following major activities, mostly from the maintenance department 1:
- testing
- servicing (operator driven maintenance, autonomous maintenance)
- restoring deterioration
- calibration
- inspection
- adjustment
- alignment (structural precision) and
- installation.
- Every maintenance team member should be familiar with these tasks and apply them accordingly.
- RCM method divides PM tasks according to their types as follows:
- TD (Time directed, Scheduled)
- TDI (time directed intrusive, Scheduled and Landed)
- CD (Condition Directed, Scheduled)
- FF (Failure finding, Bug Search)
- Programmed tasks (like replacement, discard)
- RTF (run to failure, ODM operator driven maintenance, autonomous maintenance).
The inspection methods should be carried out in accordance with the condition of the equipment. As a rule, the users of the machine who are continually operating the machine and sense its performance (normal and abnormal), should execute the inspections. The inspection routines should be designed in such a way that the operators can perform these tasks 1.
As a rule, PM is a scheduled activity that is carried out while the machine is operating as well as during planned or unplanned downtime. Preventive maintenance could also include minor improvement maintenance and the fault analysis, as they too aim to reduce equipment failure 1.
Zero Breakdowns
Figure 5 shows areas of activities included in a Zero Breakdown strategy. The starting point in avoiding failure is understanding that all defects result from changes that occur when the asset ages and when it is used. The detection of these changes is often missed, caused by contributing factors such as insufficient inspection and wear monitoring because of the design of the asset not being maintenance-friendly, or the dirtiness of the asset and hostile conditions in the working area. The second reason is the fact that the defects are accepted as part of normal operation, the impact of defects is underestimated or not considered important 1. (Explanations see: TPM – Zero Breakdowns – ForestBioFacts)
The following approach strategies can be followed in the pursuit of the failure:
- Keep the asset in shape, clean, lubricated and aligned
- Keep the asset’s operating condition in order
- Monitor the asset’s net output
- Restoring performance
- Improve the asset construction
- Trained asset users and maintenance operators. Often the cause of failure is unintentional misuse.
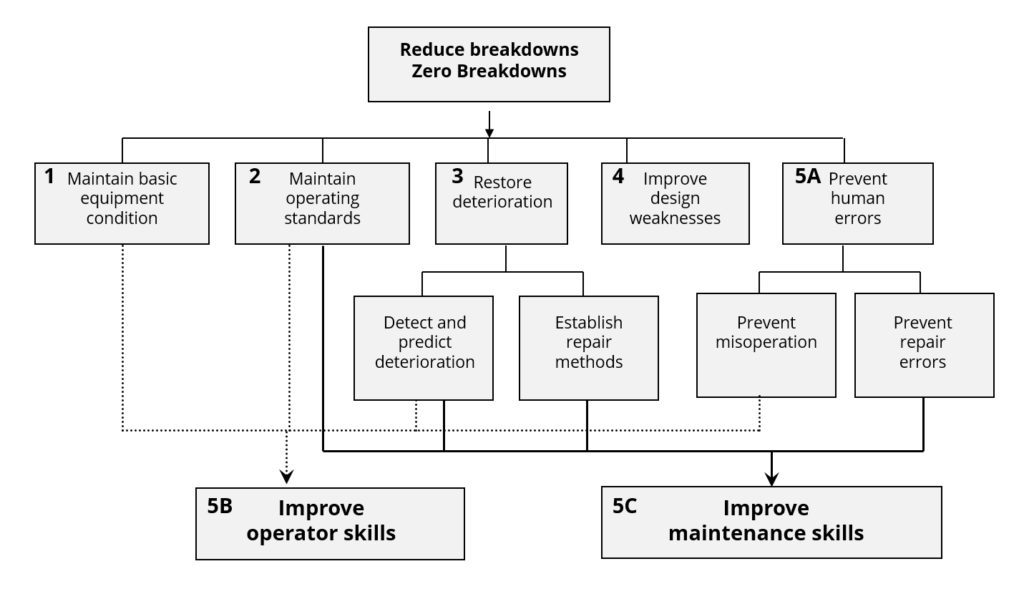
Impact of the asset care
Maintenance alone (as part of fixed asset management) is one of the largest company costs (in fact, capital and raw material costs are the largest). It is important to understand that maintenance is the largest uncontrolled cost of business. Well-managed companies have therefore invested in managing and controlling maintenance and its costs 1.
The effect of maintenance on the company’s result is both direct as well as indirect. It is necessary to know these mechanisms of action in order to determine, for example, the economic impact of maintenance and the return on maintenance investments 1.
The impact models for maintenance have been identified, for example, by professor Veli Siekkinen. The effect chain shown in Figure 6 is quite long.
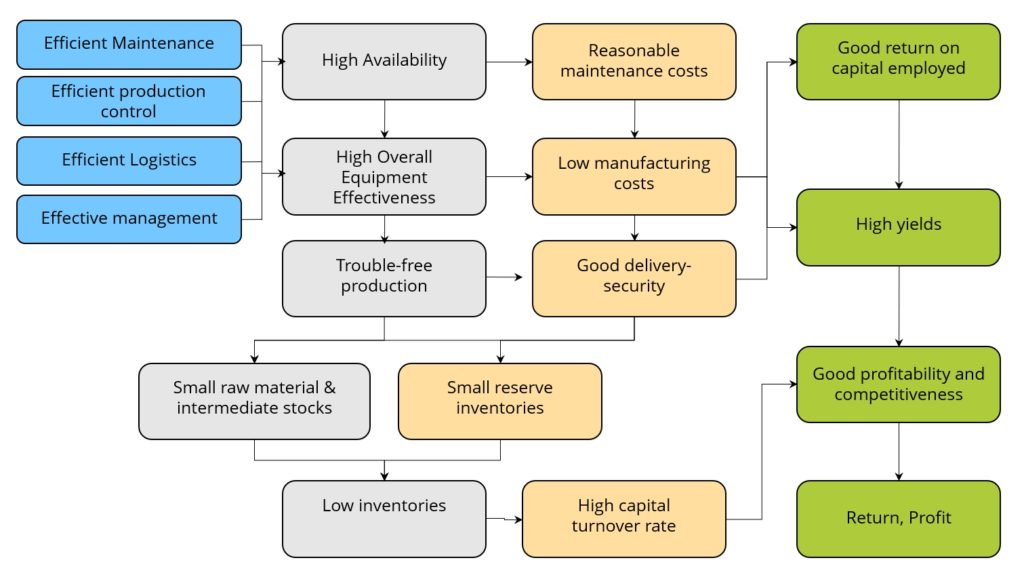
Maintenance economics
Maintenance is a business. The operation must be such that it fulfils the conditions of business, the most important of which is rationality. It should be remembered that every business must sustain competition. The task is to produce commodities and services in a productive fashion. This is also the main goal of the maintenance department. Subcontracted maintenance must be profitable if it wants to stay on the market. In-house maintenance does not generate revenue, but it must be cost-efficient in order to survive 1.
In the economic sciences, the cost structure of an enterprise can be presented in several different ways. However, this sets out the usual distribution method used in the industry for direct and indirect costs. It also presents intangible losses and costs. Non-availability costs are not handled because they are considered part of the management area 1.
Cost-causing elements are presented in Figure 7. The metrics of direct costs are caused by
- salaries and wages, etc. (labour costs)
- spare parts used
- purchasing costs
- warehousing costs
- materials, consumables used
- subcontracting, external work
- overheads, most of which are administrative fees, property costs, rents, storage costs, etc.
The direct costs of maintenance include costs incurred in maintenance. These costs can be directly attributed to maintenance. They are often budgeted. Indirect costs are difficult to allocate or cannot reasonably be allocated. Immaterial consequences are caused by poor quality of maintenance (and operation), which have other consequences that have a direct, mostly negative impact 1.
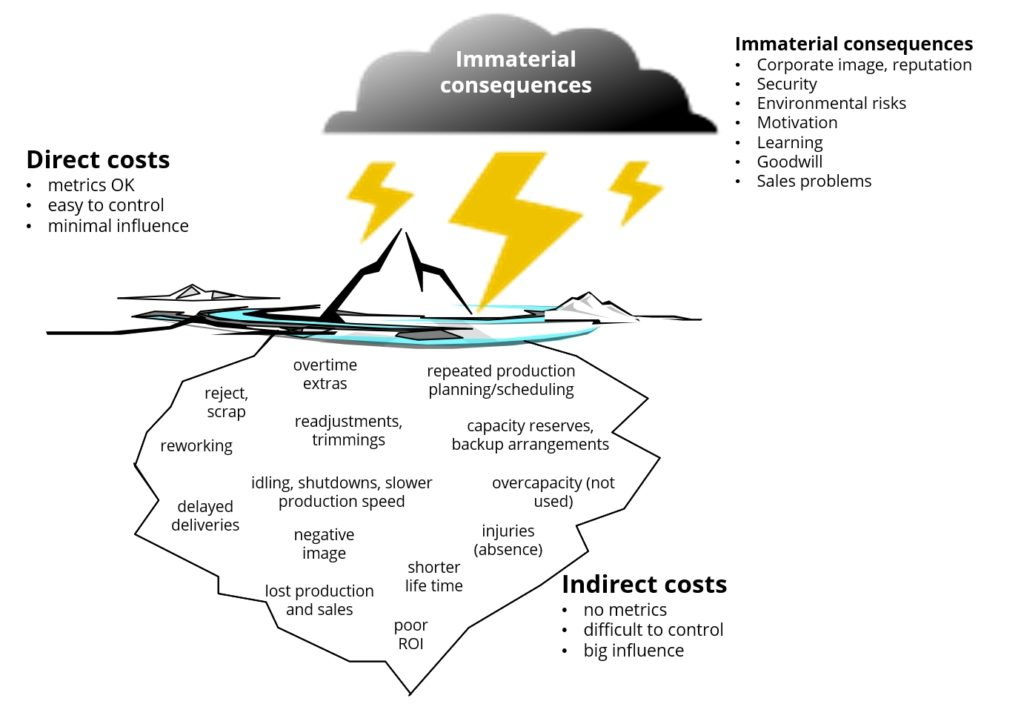
Failure prevention
British TPM expert Peter Willmott has encountered the following in his projects 9:
- 40% of failures can be prevented by keeping the operating environment clean and the machine in condition
- 20% of the defects can be eliminated by proper, daily inspection and using the machines correctly
- 25% can be prevented by an effective preventive maintenance programme and condition monitoring
- 15% of defects can be eliminated by improving machine structures and component reliability.
Maintenance organisations
Traditional organisation types are shown in Figure 8 1. The different organisation types are also listed below:
- Functional organisation, in which maintenance and resources are centralised and separate (disintegrated) from other departments of the mill.
- Divisional organisation, in which staff functions are centralised, but resources are distributed to production divisions/mills/lines, depending on the company. This type of organisation is also considered as decentralised.
- Functional organisation with central staff, in which centralised maintenance resources are managed by central staff.
- Matrix organisation, in which maintenance resources are distributed into production lines or mills that also have the managerial responsibility. This type of organisation is also known as decentralised organisation.
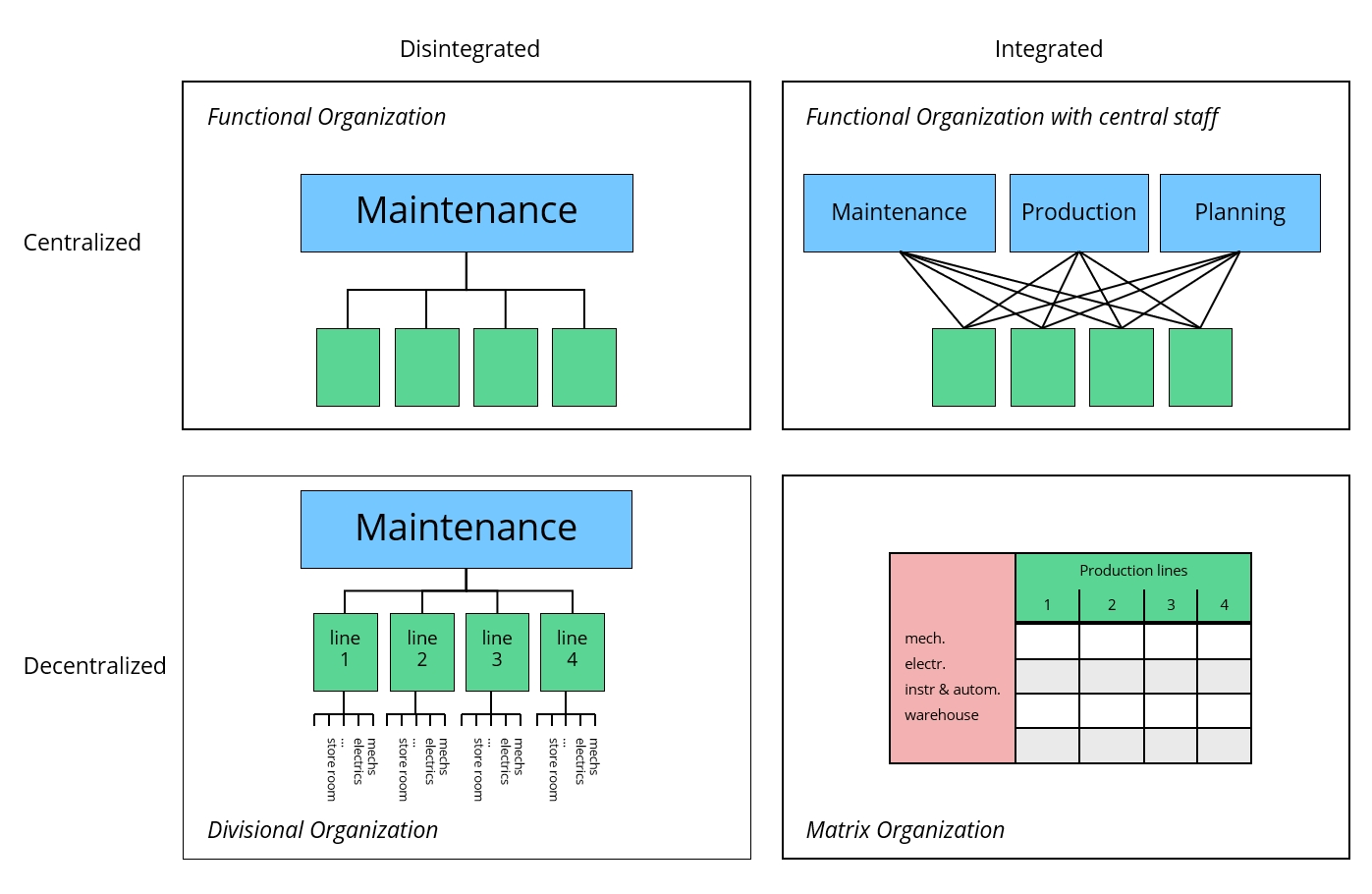
The benefits and drawbacks of different organisation types are described in more detailed in Maintenance organisations – ForestBioFacts.
The technicians, supervisors, planners, and managers must have required qualifications, essential knowledge, and minimum skills levels to be able to carry out their part in a maintenance organisation 1:
- The tasks of the service technician consist of self-contained, maintenance-oriented maintenance tasks.
- The supervisor/planner coordinates maintenance tasks within the framework of the annual budget, appropriate plans, and unplanned maintenance tasks. The supervisor/planner participates in ensuring the availability and performance of the plant in accordance with the technical availability and quality objectives of the company or unit.
- The planner works with the supervisor and supports this in defining maintenance plans, resource requirements for implementation, maintenance budget monitoring, and analysis of anomalies. The planner recommends asset management improvement projects related to usability, reliability, maintainability, and security.
- It is the responsibility of the maintenance manager to ensure that the plant is fit for purpose and performance (based on performance indicators), particularly in terms of availability and quality.
Performance culture
Technical changes such as renewal of machines or processes can be made up easily, but the adoption and implementation of new ‘habits’ takes time. In these cases, it is the old truth that the company’s learning and the speed of the change is the same as its slowest man. The ability to change in modern society is important. The need for change together with the speed of change will increase 1.
A new element has been added to business management. It is called Performance Culture, the main elements of which are:
- the correct performance indicators,
- the implementation of the economic results (KPI), and
- the use of changes and the associated use in performance measurement.
Measuring the performance as well as the financial result are tasks of the management, but the behavioural changes are measured from the factory floor.
The areas shown in the circles of Figure 9 have previously been treated as their own discipline and competence area. In a performance culture, performance consists of a shared area where all these elements work together.
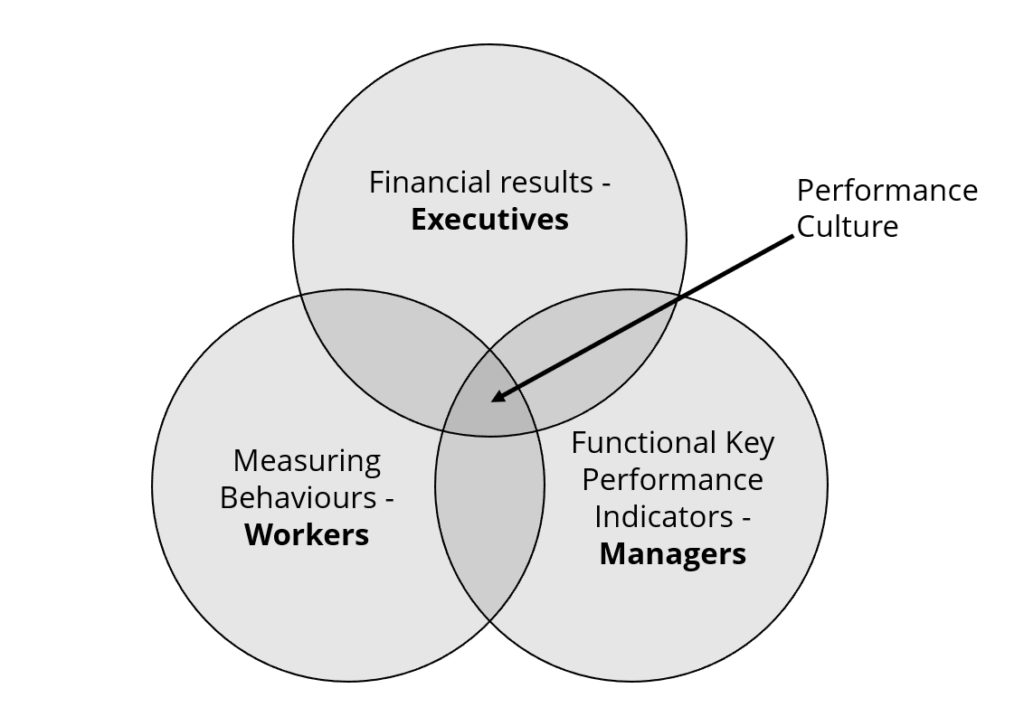
Benchmarking
Benchmarking means comparing your activities to the activities of others, often in the best practice. The basic idea behind benchmarking is learning from others and questioning your activity. It is a continuous systematic comparison of the organisation’s productivity, quality, work processes and working habits with the corresponding companies and organisations representing the categories 1.
The main types of benchmarking are:
- internal benchmarking
- competitor benchmarking
- operational benchmarking (for companies operating in the same sector)
- benchmark independent of industry.
Benchmarking activities are commonly used in the business world and often specifically as a tool for developing quality systems and process development. Benchmarking helps identify weaknesses in your activity and develop goals for their development and come up with ideas for development. Benchmarking can be a comparison of strategies, processes, or data (metrics).